The combination of the Camfil 30/30 MERV 8A prefilter and Hi-Flo ES 22″ deep MERV 13A pocket final air filter saved $33,000 annually for a top American frozen food manufacturer.
After 45-days of testing air filters in two identical air handling units, an independent third-party consultant measured significant energy savings with Camfil air filtration products in one of America’s largest frozen food manufacturing facilities. The air filters used for this test pitted the Camfil 30/30 MERV 8A prefilter and the Hi-Flo ES 22″ deep MERV 13A pocket final air filter against a competitive MERV 8 pleated prefilter and MERV 11 synthetically-charged media final air filter.
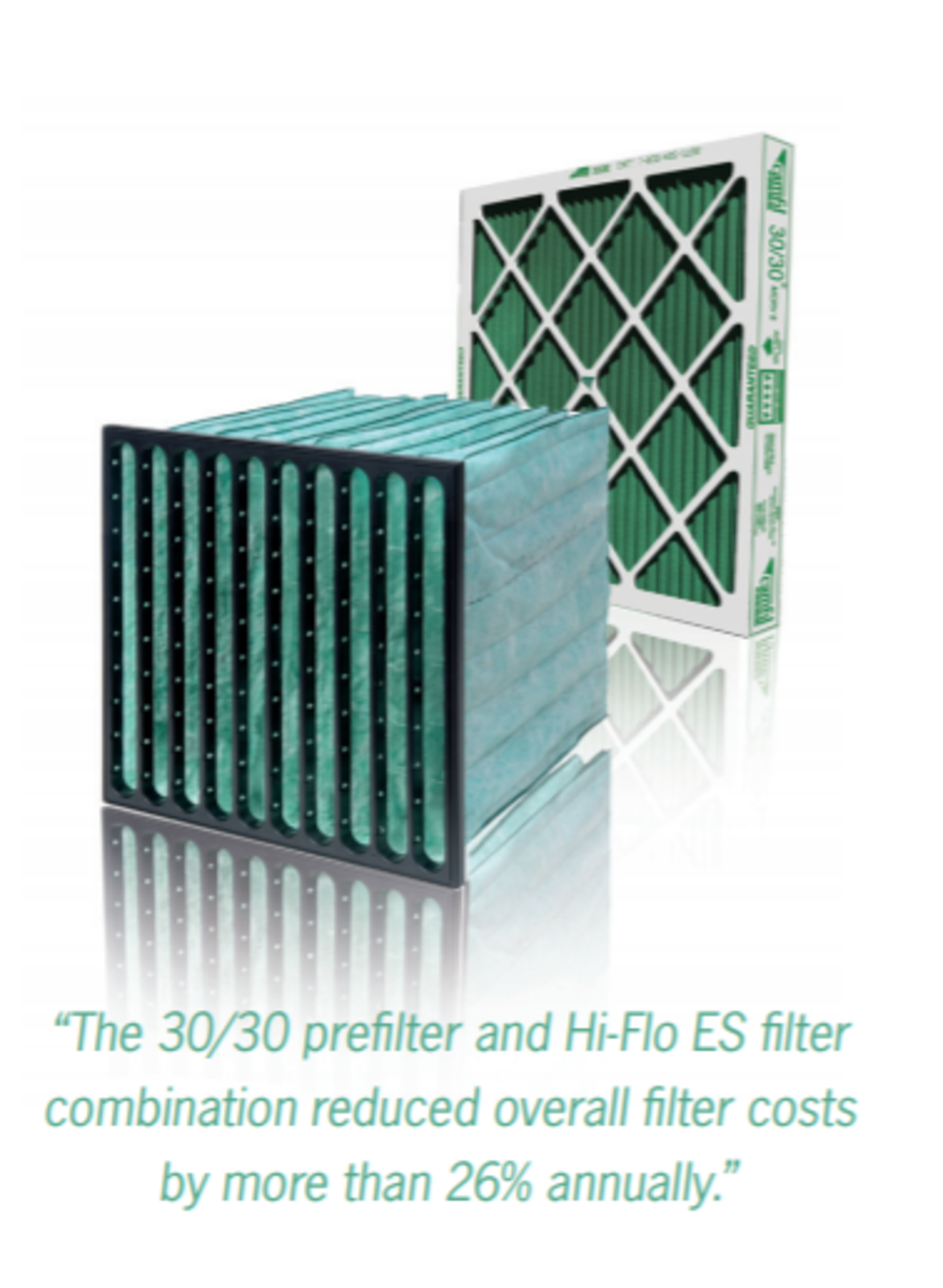
The case study found that “The high moisture return air contained breading residue which restricted airflow and overwhelmed the competitive MERV 8 pleated prefilter within one to two weeks.”
The inability of the competitive filters to adequately supply air to the facility’s critical processing areas resulted in the need to frequently change the air filters in their large rooftop air handling units.
What’s more, because the MERV 11 competitive filter utilized synthetically-charged media, the final filter would lose particle capture efficiency (MERV value) the longer it remained in service. The net effect of this was the air filters that were the incorrect efficiency for the critical application, to begin with, would be even less efficient as time passed. Additionally, the competitive final filter was only four inches in depth, which meant there was insufficient media area for the high dirt-loading application causing the filter to quickly reach its dirt holding capacity.
Along with longer service life and reduced labor and disposal fees, the Camfil air filters also provided a significant energy reduction due to their low average pressure drop. As dirt accumulates on an air filter, airflow is restricted. Air volume is crucial in a critical process such as food processing, so fans are programmed in order to increase speed to maintain the proper airflow. The design of the Camfil air filters allow far more dirt to accumulate before an adjustment to fan speed is required. The reduced fan speed translated into substantial cost savings. The average cost of energy for the unit operating with the Camfil MERV 8A prefilter was $37.86 per day, as opposed to $42.67 per day for the unit running with the competitive pleated prefilter.
“The Camfil 30/30 MERV 8A prefilter and Hi-Flo ES 22” deep MERV 13A pocket final filter combination was the perfect solution — and saved this particular facility over $33,000 annually,” stated Patrick Lally, Food and Beverage Segment Managers at Camfil USA.
About
Camfil is the world leader in air filtration and clean air solutions, which has 30 production plants and R&D centers in the Americas, Europe, and the Asia-Pacific region. For more information, visit us online at www.camfil.us or call us toll-free at 888.599.6620.
Media Contact:
Lynne Laake
Camfil USA Air Filters
T: 888.599.6620
E: Lynne.Laake@camfil.com
F: Friend Camfil USA on Facebook
T: Follow Camfil USA on Twitter
Y: Watch Camfil Videos on YouTube
The post Case Study: Camfil Filters Provide Significant Energy Savings for a Leading American Frozen Food Manufacturer appeared first on Air Filters for Clean Air.